收錄于話題
#APQP-項目管理60個內容
#FMEA失效模式及后果分析128個內容
當PFMEA分析時,失效原因是產品設計問題如何辦?

在APQP第二階段,進行DFMEA分析時,除了分析主功能之外,還要進行可制造、可裝配功能的風險分析,然后通過樣件試裝來驗證,在輸出A版圖紙時,應組織工藝、設備、質量、生產等跨部門的人員進行DFMA制造可行性評審,站在供應商和制造商的角度對生產資源和產品設計提出優化,實現質量的同時,提升生產和裝配效率。
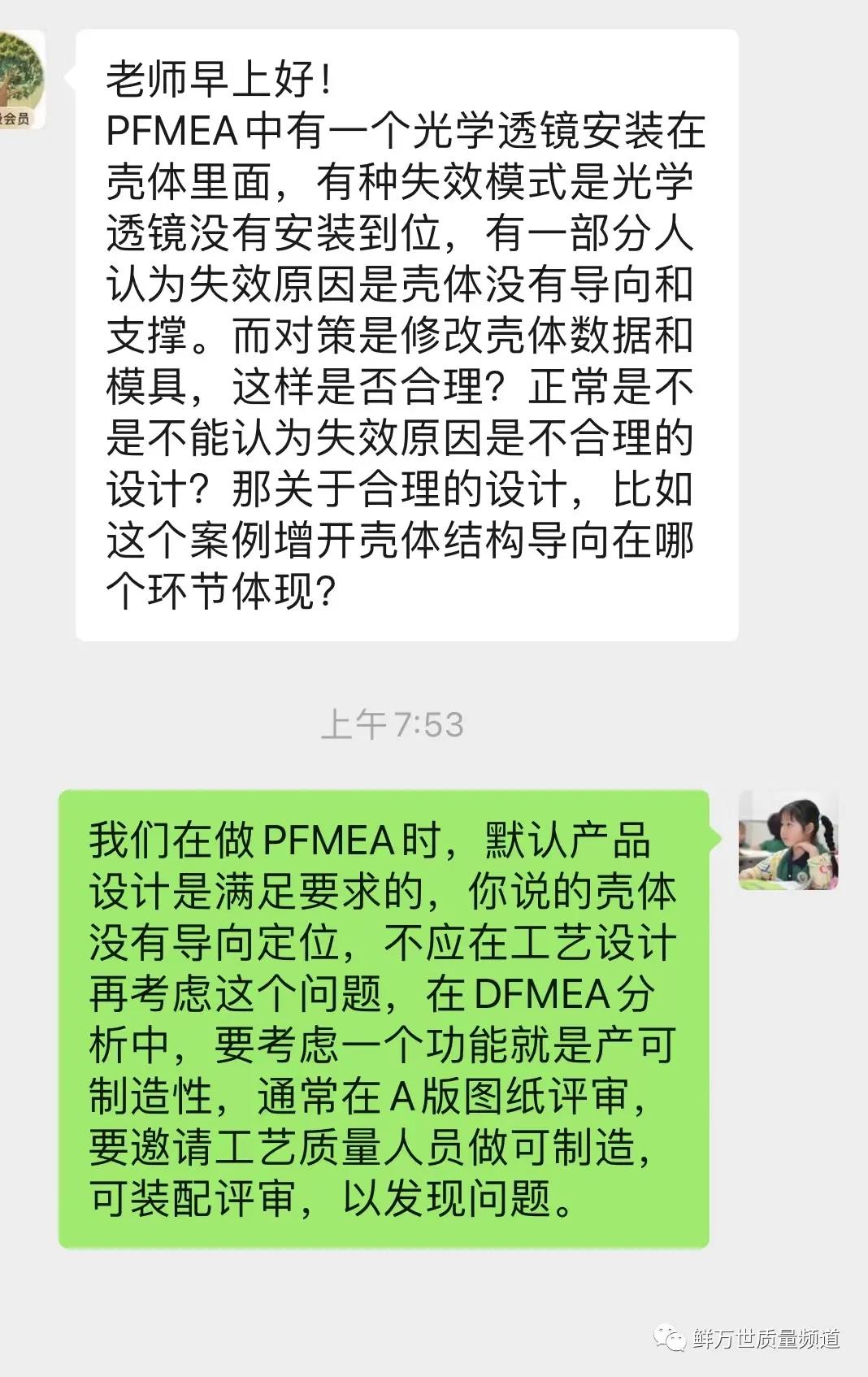
話說前兩天在群里說,PFMEA中有一個光學透鏡安裝在殼體里面,有種失效模式是光學透鏡沒有安裝到位,有一部分人認為失效原因是殼體沒有導向和支撐。而對策是修改殼體數據和模具,這樣是否合理?正常是不是不能認為失效原因是不合理的設計?那關于合理的設計,比如這個案例增開殼體結構導向在哪個環節體現?但也有人認為,這不是PFMEA的考慮的內容。為什么會有這樣的爭論呢?鮮老師你怎么看?
先說我的觀點,我認為之所以會出現這樣的爭論,還是沒搞清楚DFMEA與PFMEA之間的邏輯關系。我們在做PFMEA時,默認產品設計是滿足要求的,你說的殼體沒有導向定位,不應在工藝設計再考慮這個問題,在DFMEA分析中,要考慮一個功能就是產品可制造性,通常在A版圖紙評審時,要邀請工藝,生產,設備,質量人員做可制造,可裝配評審,以發現問題及時整改,確保可制造性。在APQP的第二階段,DFMEA的七步法中的第三步功能分析,具體的功能分析包括基本功能、輔助功能和非功能,基本功能是系統要素預期的輸出,比如起動機的基本功能是起動發動機,輸出飛輪扭力和轉速,其中輔助功能有接口功能、自診斷功能、自保護功能、防傷害功能、可維護功能、可制造功能、可裝配功能??芍圃煨怨δ苁遣捎靡话愠R姽に囘^程可以完成,可裝配功能是能裝配,裝配效率好,質量好。非功能是約束功能,就是限制設計自由度的功能,如限制空間尺寸。
我們就微信群里聊的“光學透鏡”,進行案例分析,由于缺少技術支持,我就點到為止說明一下方法論,技術上的不成熟希望大家補充。有一個光學透鏡安裝在殼體里面,光學透鏡沒有安裝到位,原因是殼體沒有導向和支撐,對策是修改殼體數據和模具,此過程不應在PFMEA中分析,應在DFMEA中分析。嚴重度:7分(由于失效后果是主要功能下降,所以評7分)預防措施:對標設計、參考設計標準XX殼體外觀導向與定位要求發生度:3分(因為有參考外殼導向與定位設計標準,有設計參考評為3分)
探測度:4分(使用原型樣件進行試裝,是一種通過/不通過的驗證手段)術業有專攻,DFMEA主要是用于主功能的失效分析,針對可制造性功能也適用,但效果一般,我們可以用專用的工具來處理與分析這個問題,就是DFM可制造性設計、DMA可裝配性設計。
在完成DFMEA分析后,輸出潛在的特性清單及DV設計驗證計劃,然后輸出的初始版本(A版)的圖紙、技術規范,需要召集工藝、質量、生產等人員進行可制造、可裝配性評審。具體可以見以前寫過的一篇文章《產品開發過程中有哪些質量管理(工具)方法論?》DFMA: Design for Manufacture and Assembly DFMA / DFMAS包括下述方法: DFM: Design for Manufacture 該方法的目的是通過確保面向制造和服務的產品設計而降低成本,及減少制造方面的缺陷,從而減少少出現使用缺陷,由此而降低保修成本,并: KISS原則(Keep It Simple, Stupid):產品的設計越簡 單越好,簡單就是美,任何沒有的復雜都是需要避免的。《喬布斯傳》Jonathan Ive:“只要不是的部件,我們都想辦法去掉”,“為達成這一目標,就需要設計師, 產品開發人員,工程師以及制造團隊的通力合作。我們一次次地返回到最初,不斷問自己:我們需要那個部分嗎? 我們能用它來實現其它部分的功能嗎?”最的產品是沒有零件的產品;產品設計得復雜,是一件簡單的事情;把產品設計得簡單,是一件復雜的事情。
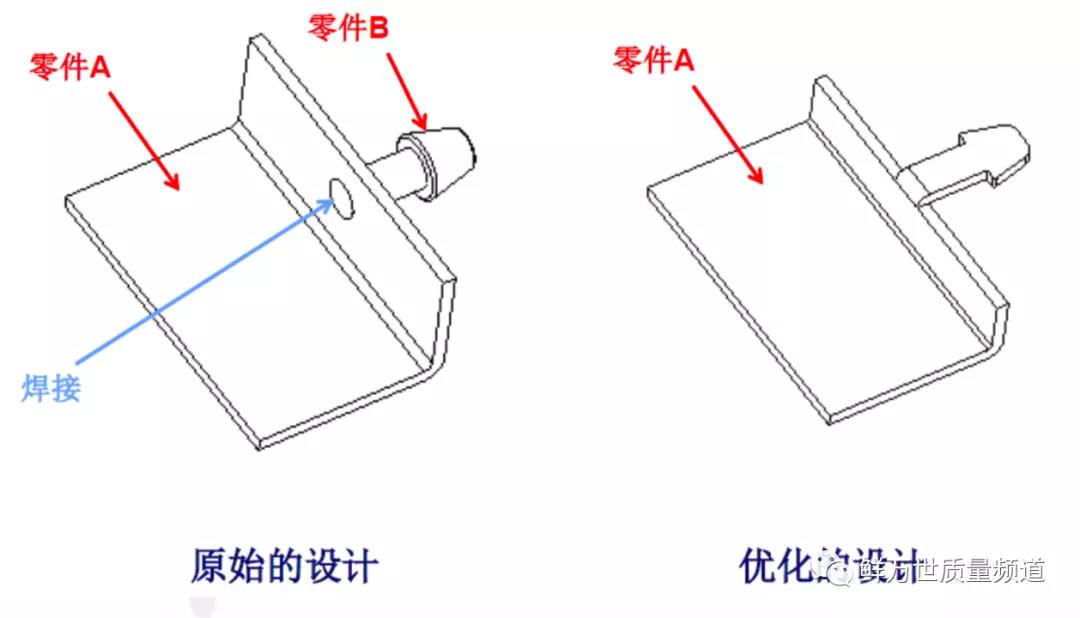
該方法屬于面向小組的質量方法。因此有讓設計開發、策劃和制造等相關部門的代表參加小組會議。1.在小組會議上,主持人和參與者利用在方法中確定的提問技巧確定一個部件中每個零件的功能。2.然后提問,如果為了使制造和裝配工作更簡單而將這些零件合并/或簡化,是否還能達到該功能。3.這個過程應使用標準化的設計檢查表。
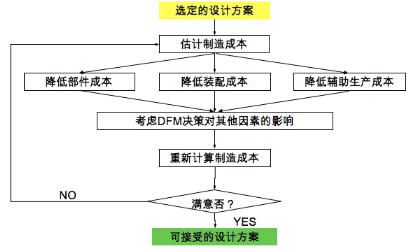
針對產品詳細的設計輸出,圖紙、產品特性清單、產品BOM等進行制造可行性分析,站在自制件或外包供應商的角度進行生產資源、檢測資源及經濟性分析,可以結合DFMA可裝性和可裝配設計一起進行可行性分析,一般可包括:
一個組件或系統都有自制件,塑膠件是注塑工藝,工藝工程師對自制件進行制造可行性分析,如果為外包,由SQE與供應商共同完成制造可行性分析,產品的可注塑性分析包括如下:-加強筋的厚度不應超過塑膠零件厚度的50%-60%;
產品可鑄造性分析包括如下:
-產品結構應能合理設置模線,無拔模死角;
-各鑄造面應保證的拔模斜度;
-壁厚過度應均勻,避免產生疏松和開裂現象;
-圓角半徑不宜過小,避免應力集中;
-粗基準設置應利于加工定位、夾緊,同時可保證關鍵部件的相對鑄造精度。
-···
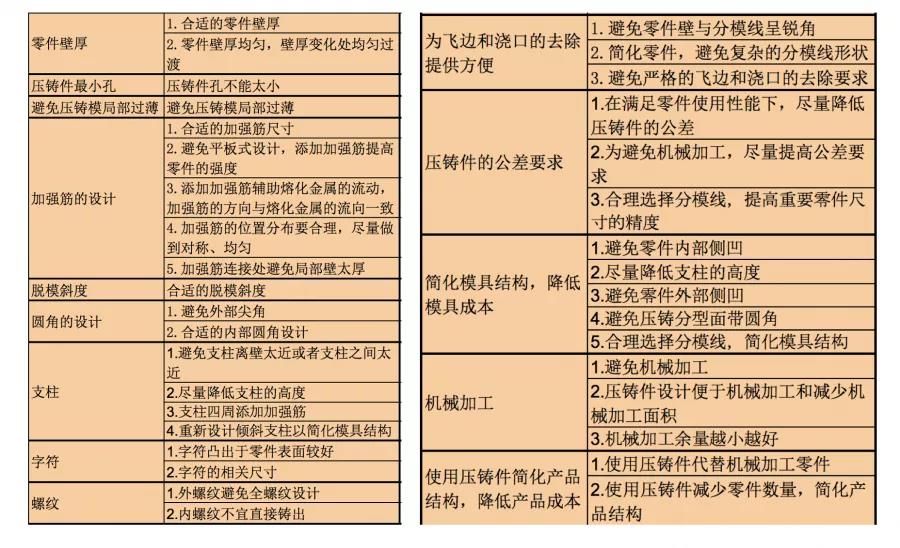
產品裝配性分析包括如下:
-減少零件數量;
-減少緊固件的種類和數量;
-零件標準化;
-產品模塊化;
-零件容易被抓??;
-····
總的來說,在詳細設計后的制造可行性分析,一般針對每一個零件或組裝,結合DFMA進行計算分析、模擬過程驗證,對生產設備工裝及檢測資源進行分析,站在供應商和制造商的角度對生產資源和產品設計提出優化,實現質量的同時,提升生產和裝配效率。
綜上所述,鮮老師認為在APQP第二階段,進行DFMEA分析時,除了分析主功能之外,還要進行可制造、可裝配功能的風險分析,然后通過樣件試裝來驗證,在輸出A版圖紙時,應組織工藝、質量、生產等跨部門的人員進行DFMA制造可行性評審,站在供應商和制造商的角度對生產資源和產品設計提出優化,實現質量的同時,提升生產和裝配效率。
作者簡介:
鮮萬世:TUV萊茵FMEA專家之一,微信公眾號主編,FMEA相關原創技術文章200多篇。在歐美日世界500強制造業集團公司,相關質量管理的經驗超過10年;擅長于汽車制造系統及其零部件制造與質量改進項目的培訓與咨詢·;建立了精益成熟度評價系統,并為上汽大眾汽車、延鋒偉世通建立了精益評估系統;擅長FMEA、ISO9001、IATF16949等與質量有關的管理體系以及質量改進的工具應用。